企画から納品まで、全ての工程を手がけます。
一般的に分業体制が多い陶磁器の生産において、私たちは商品の企画デザインから製造まで全てを一貫して自社内で行います。より新しいモノを、より早く、より高い技術をもってカタチにできる。そんな事を実現できる体制を整えています。
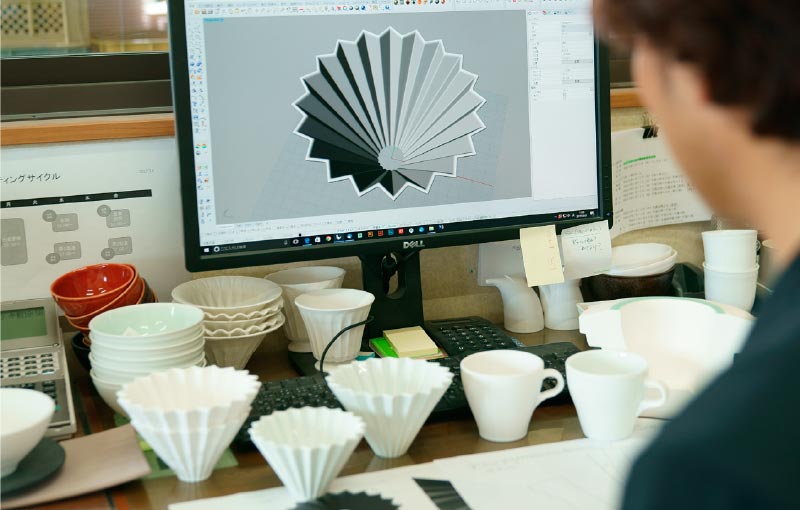
step 1.
企画・サンプル製作
自社商品のコンセプトに合わせた企画・デザインを常時行っております。形状のデザインから色柄を付けた最終デザインまでを一貫して行っており、人の手で描く感性を生かしたデザインと、CAD等のデザインソフトを使用してのプロダクト的なデザインの両方を組み合わせながらアイデアを形にしていきます。お客様から依頼のオリジナル企画・デザインも随時行っております。
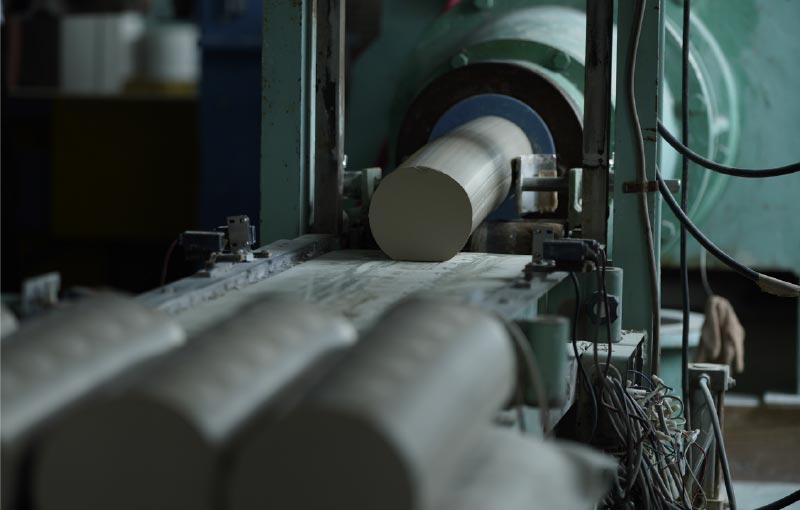
step 2.
土練り
原料の土を均一に混ぜ合わせ、土の中にある気泡を抜きながら、練ります。一定量の水分を混ぜる事で土の可塑性を出します。白さと透光性を兼ね備えた白磁土、強度を持った強化磁器土、直接火に掛ける事ができる耐熱土など常時8種類ほどの土を常備し製造を行っています。
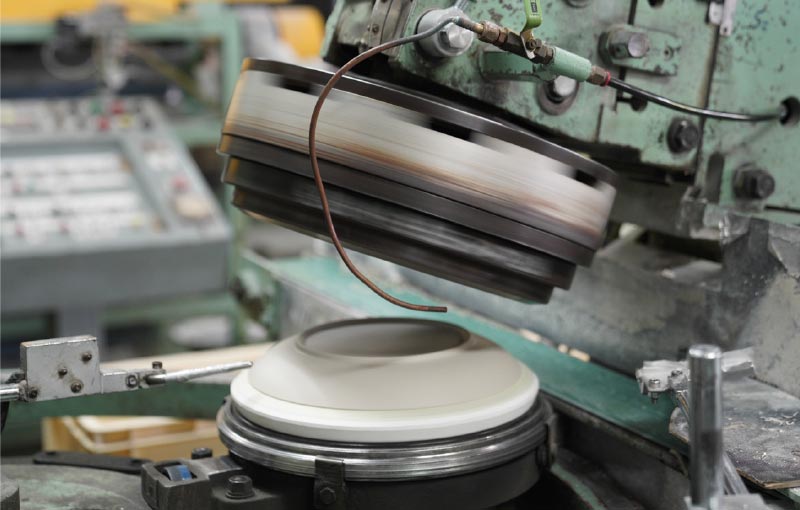
step 3.
成形
大きく分けて土を回転させながら引き延ばし成形していくロクロ成形、泥状にした土を型に流し込むことで成形する鋳込み成形があります。丸い円形をしたプレート、ボウル、カップなどはロクロ成形で、その他スクエアーやオーバルなどの回転で作れない形状は鋳込み成形で作られます。
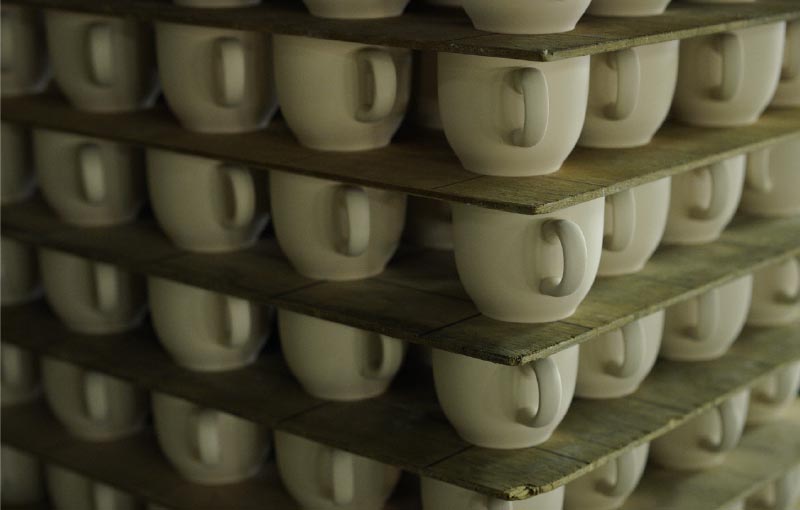
step 4.
素焼き
成形した製品を一度低温の800度で焼成を行います。土の中にある有機物を焼き切ることでその後の本焼成でのクオリティを上げたり、低温で焼き生地を硬化させることで加飾を行いやすくします。
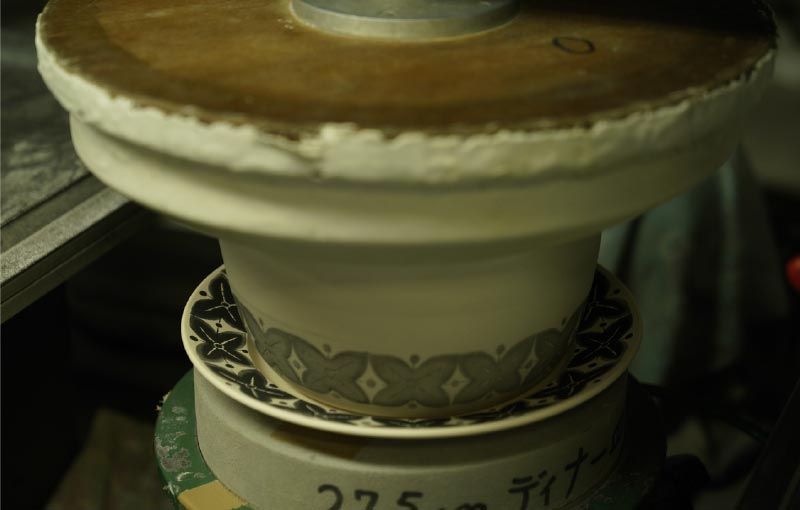
step 5.
下絵付け
パッド印刷、スクリーン印刷と呼ばれる印刷方法や手での加飾で生地に柄を付けていきます。繊細な柄の印刷から、暖かみのある筆での加飾まで幅広く商品のスタイルに合わせて色、柄を付けていきます。
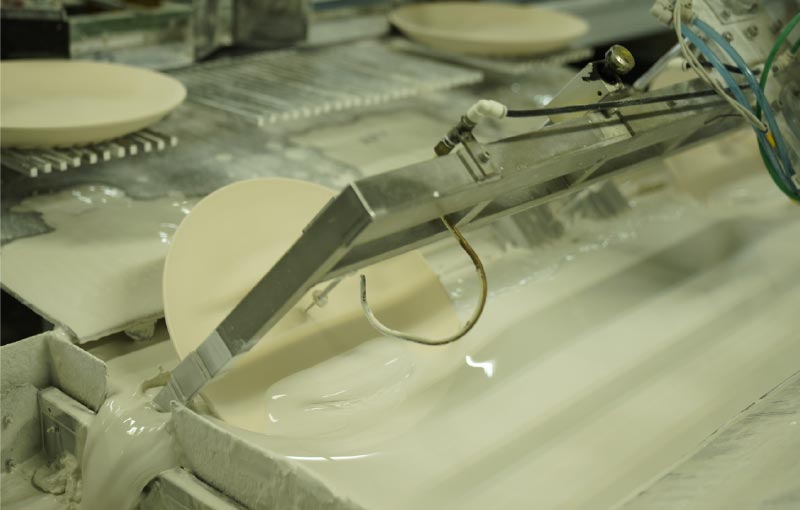
step 6.
釉薬かけ
釉薬と呼ばれるガラス質の粉を生地に塗布していきます。液状に見える釉薬ですが、ガラス質の粉が水に溶かしてあり、ここに生地を浸ける事で水分が生地に吸収され、ガラスの粉が生地の表面に薄い膜で付着します。釉薬はその色、表面の表情で無限のバリエーションが存在します。私たちは数百種類のレシピを持ちながら、商品のスタイルに合わせそれらを組み合わせていきます。
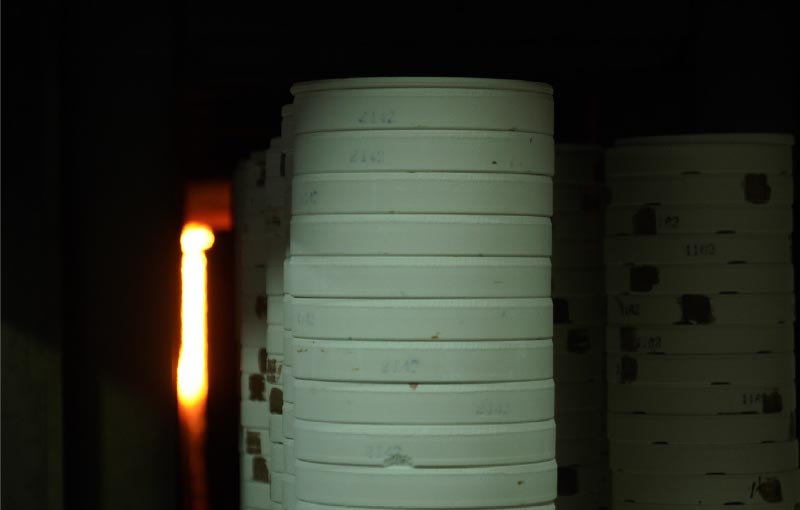
step 7.
本焼成
酸素を十分に供給させて1250℃で焼成する”酸化焼成”と酸素を絞った状態で1320℃で焼成する”還元焼成”の両方を常時トンネル窯で稼働させています。豊富な加飾や釉薬に加え、多彩な色の発色が可能な酸化焼成と、この焼成方法でしか出せない特有な色の発色が可能な還元焼成の2つの焼成を常時稼働させている事により、幅広いデザインの表現、商品供給を実現させます。
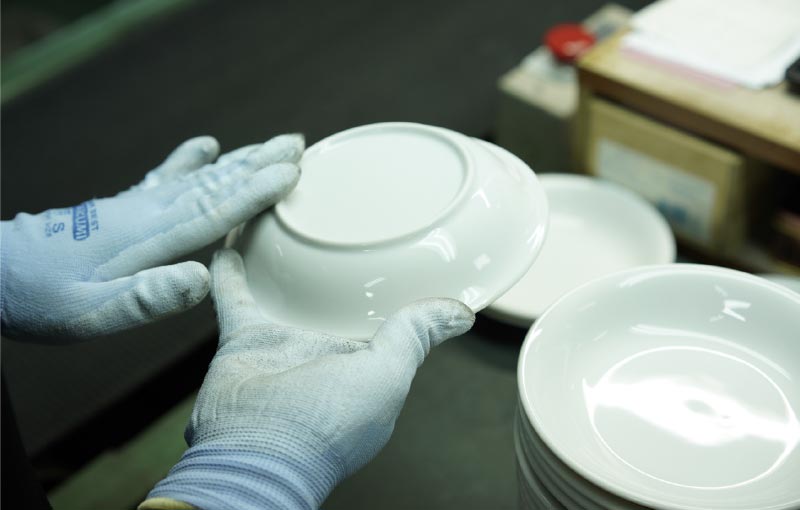
step 8.
検品
製造が完了した製品は全て人間の目で一つ一つ検品されます。プロフェッショナル向けの厳しい品質基準をクリアした製品のみが、皆様の手元に届けられます。
設備紹介
多品種少量生産をベースにしながらも数万個の大きなオーダーにも対応できる柔軟な生産体制、バリエーション豊かな商品ラインナップを支える設備です。
-
土練機
素材となる土を練り、成形できる状態にします。土練機ごとに異なる土に対応しており、現在は磁器土、並土、強化土、耐熱土など機能やグレード(品質)に応じた8種類の土を使用しています。
-
自動成形機
土練機で練られた土を、器の形にロクロ成形します。成形、乾燥、バリ仕上げまで全自動で行うラインで、成形能力は1台につき最大約3000個/日。主に中・大ロットでの成形に対応します。
-
単体成形機
ロクロ成形のみをマシンで行い、バリ仕上げなどは人間の手で行います。成形能力は1台につき最大約2000個/日。小ロットでの成形、さらには短納期での成形にも柔軟に対応できます。
-
鋳込み設備
ロクロ成形では対応できない形状の器を、型に土を流し込んで成形します。乾燥に一定の時間を要するため、成形能力は1台につき最大約500個/日。特殊な形状の器でも成形が可能です。
-
パッド印刷機
下絵付けを行う印刷機です。シリコンでできたパッドに、柄に乗った絵の具を写し取り、素焼きされた器に押し付けて印刷します。印刷能力は1台につき最大約1,000個/日。小ロットでの対応も可能です。
-
釉薬ライン
器の印象を決める釉薬をのせます。光洋陶器では常時300近い釉薬が保管されており、製品やお客さまのご要望に合わせて組み合わせていきます。自動化ラインと人の手で行うラインを製品に応じて使い分け、柔軟な生産計画を立案します。
-
焼成炉
(素焼きトンネルキルン)
素焼きを行う窯です。約800度の低温で30時間近くかけて焼成を行います。
※大型連休を除き、1年中24時間稼働しています。 -
焼成炉
(酸化焼成トンネルキルン)
本焼成を行う窯です。酸化焼成とは、酸素を十分に供給する焼成方法で、約1,250℃の高温で30時間近くかけて焼成を行います。焼成方法によって釉薬の反応が異なるため、釉薬の発色に合わせて還元焼成の窯と使い分けます。
※大型連休を除き、1年中24時間稼働しています。 -
焼成炉
(還元焼成トンネルキルン)
本焼成を行う窯です。還元焼成とは、酸素を意図的に減らす焼成方法で、酸化焼成よりも高温の1320℃で20時間近くかけて焼成を行います。器に用いる釉薬によって、酸化焼成と使い分けます。
※大型連休を除き、1年中24時間稼働しています。
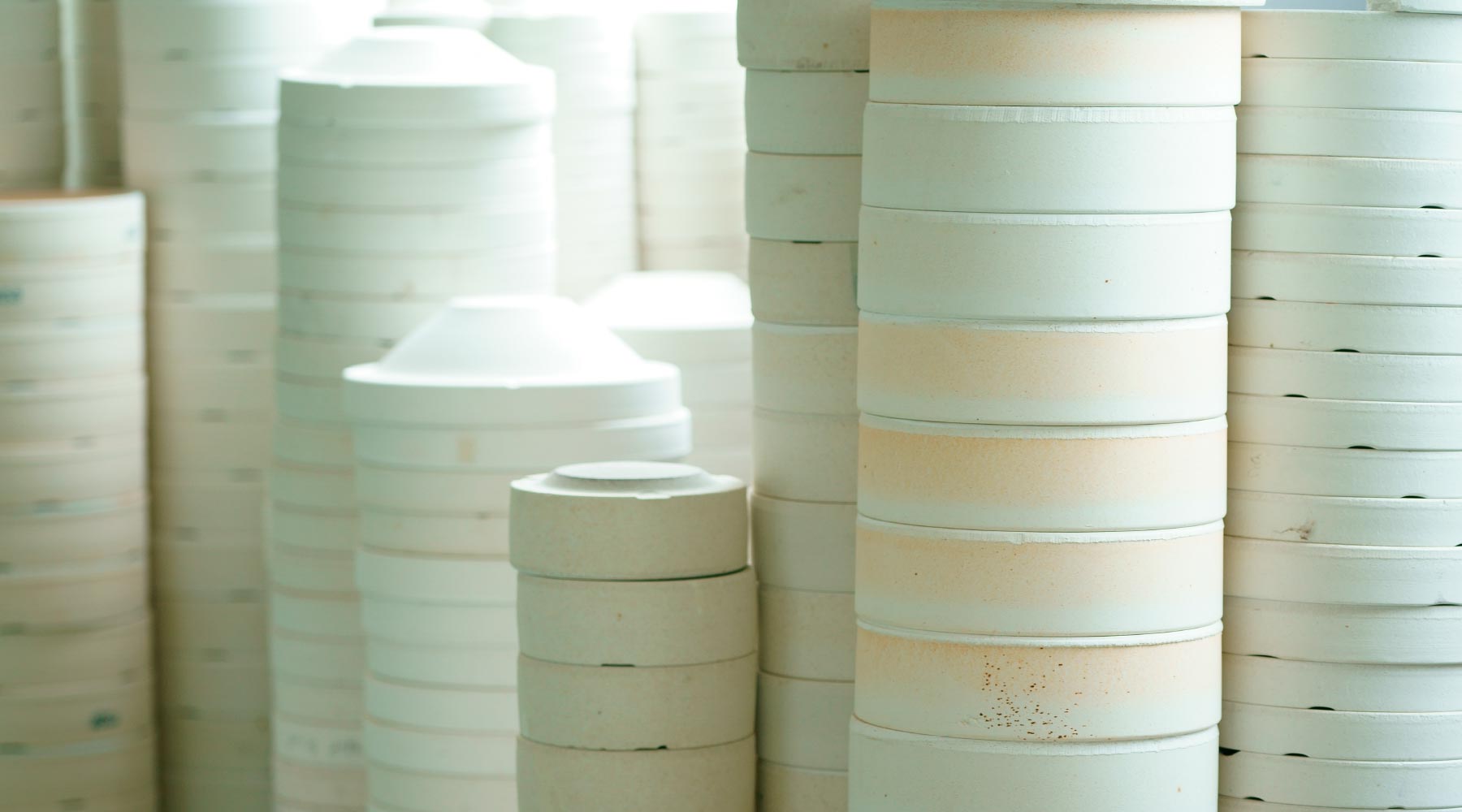